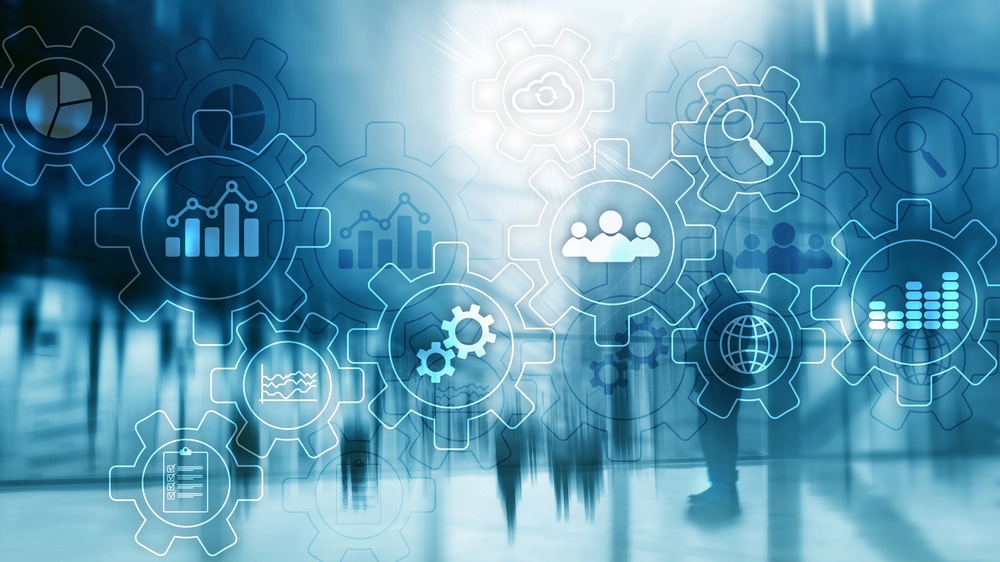
A Relevância do FMEA na Prevenção de Falhas em Processos Industriais
O FMEA (Análise dos Modos de Falha e seus Efeitos) é uma metodologia sistemática utilizada para identificar potenciais modos de falha em processos e produtos. Essa análise visa avaliar os efeitos dessas falhas e propor ações corretivas antes que ocorram. Na indústria moderna, o FMEA se destaca como uma ferramenta essencial para garantir a qualidade e a confiabilidade dos processos industriais.
Com a crescente complexidade dos sistemas de produção, a implementação do FMEA torna-se ainda mais relevante para a prevenção de falhas e a redução de riscos. Este artigo tem como objetivo explorar a relevância do FMEA na prevenção de falhas, destacando suas vantagens, melhores práticas e desafios na aplicação.
Histórico do FMEA
O FMEA surgiu nos anos 1940, desenvolvido pela indústria militar dos Estados Unidos para melhorar a confiabilidade dos sistemas durante a Segunda Guerra Mundial. Com o passar do tempo, a metodologia foi adaptada e expandida para outras áreas, como a indústria automotiva, onde a Ford Motor Company foi uma das pioneiras na aplicação do FMEA nos anos 1970.
Inicialmente, o FMEA foi adotado para identificar possíveis falhas em componentes críticos de veículos, garantindo assim a segurança e a qualidade dos produtos. Com resultados positivos, a prática foi reconhecida por sua eficácia e, gradualmente, se tornou uma prática padrão em várias indústrias.
Hoje, o FMEA é amplamente utilizado em setores como aeroespacial, médico e manufatura, sendo integrado aos processos de desenvolvimento e gerenciamento de qualidade. Este avanço histórico destaca a importância do FMEA na mitigação de riscos e na promoção de melhorias contínuas nos processos industriais.
Objetivos do FMEA
O FMEA tem como principais objetivos garantir a eficácia dos processos industriais e minimizar falhas. Primeiramente, ele busca identificar modos de falha potenciais. Isso envolve a análise detalhada de cada componente ou etapa do processo para detectar antecipadamente onde podem ocorrer problemas.
Em seguida, é crucial avaliar os efeitos das falhas. Compreender o impacto potencial de cada falha permite às organizações medir a gravidade e a frequência com que essas falhas podem ocorrer, possibilitando uma visão clara dos riscos envolvidos.
Por fim, o FMEA visa priorizar ações corretivas. Após identificar e avaliar os modos de falha, é necessário definir quais ações devem ser implementadas para mitigar os riscos, garantindo que os recursos sejam alocados de forma eficiente para resolver as falhas mais críticas.
Vantagens do FMEA
O FMEA oferece diversas vantagens para a indústria, começando pela redução de riscos. Ao identificar e avaliar modos de falha potenciais, as organizações podem implementar ações preventivas, diminuindo a probabilidade de falhas críticas. Por exemplo, uma fábrica de automóveis pode utilizar o FMEA para detectar problemas potenciais em componentes antes que eles afetem a produção.
Outra vantagem significativa é a melhoria na qualidade do produto. O FMEA ajuda a garantir que os produtos atendam a padrões de qualidade elevados, identificando áreas que precisam de melhorias. Isso é essencial para manter a competitividade no mercado e para evitar retrabalhos e desperdícios.
Além disso, o FMEA contribui para o aumento da satisfação do cliente. Produtos de alta qualidade e processos eficientes levam a menos falhas e reclamações, resultando em clientes mais satisfeitos. Por exemplo, uma empresa de eletrônicos que utiliza o FMEA pode melhorar a confiabilidade de seus dispositivos, aumentando a confiança do consumidor.
Processo de Implementação do FMEA
Passos Fundamentais para Implementação
Iniciar o processo de FMEA requer uma abordagem estruturada. Primeiro, defina o escopo e objetivos claros para a análise. Forme uma equipe multidisciplinar para garantir perspectivas variadas. Em seguida, identifique todos os componentes do processo e possíveis modos de falha. Avalie os efeitos e priorize as ações corretivas com base na severidade e probabilidade das falhas.
Ferramentas e Recursos Necessários
Para uma implementação eficaz, utilize planilhas específicas de FMEA ou software dedicado, que facilitam a organização e análise dos dados. A formação contínua da equipe sobre as melhores práticas do FMEA é crucial. Recursos adicionais, como bancos de dados de falhas anteriores, também são valiosos para prever e mitigar riscos futuros.
Desafios Comuns e Como Superá-los
Os desafios na implementação do FMEA incluem a resistência à mudança e a limitação de recursos. Para superar esses obstáculos, promova uma cultura organizacional que valorize a melhoria contínua e a colaboração. Incentive a comunicação aberta e forneça treinamento adequado para a equipe. Além disso, alinhe os objetivos do FMEA com os objetivos estratégicos da organização para garantir apoio gerencial.
Estudo de Caso: Sucesso do FMEA
Uma renomada empresa automotiva enfrentava desafios frequentes com falhas em seu processo de montagem, o que afetava a qualidade final dos veículos. Para resolver esses problemas, a empresa decidiu implementar o FMEA como parte de sua estratégia de melhoria contínua. A equipe multidisciplinar foi formada, abrangendo engenheiros, gerentes de produção e especialistas em qualidade, que se reuniram para mapear os possíveis modos de falha no processo de montagem.
Após a implementação do FMEA, a empresa observou uma redução significativa nas falhas de produção, resultando em uma melhoria de 30% na qualidade dos produtos. Além disso, o índice de satisfação do cliente aumentou consideravelmente, uma vez que os veículos passaram a apresentar menos defeitos e maior confiabilidade.
As lições aprendidas com esse estudo de caso enfatizam a importância do envolvimento de todos os departamentos na análise e a necessidade de atualização contínua do processo de FMEA. A empresa também destacou a relevância de integrar o FMEA com outras práticas de gestão de qualidade para maximizar os resultados. Este exemplo ilustra como o FMEA pode ser uma ferramenta poderosa na prevenção de falhas e na melhoria da qualidade em processos industriais.
Melhores Práticas para FMEA
Para garantir o sucesso da implementação do FMEA, é essencial adotar algumas práticas recomendadas que aumentem sua eficácia.
- Envolvimento de equipes multidisciplinares: Incluir profissionais de diferentes áreas, como engenharia, produção e qualidade, garante uma visão abrangente dos modos de falha potenciais. Essa diversidade de perspectivas ajuda a identificar e analisar riscos que poderiam passar despercebidos por uma equipe homogênea.
- Atualização contínua do processo: O FMEA não deve ser um documento estático. É importante revisá-lo e atualizá-lo regularmente para incorporar novos dados e mudanças nos processos. Isso mantém a análise relevante e eficaz na prevenção de falhas.
- Uso de software especializado: Ferramentas de software podem facilitar o registro, acompanhamento e análise dos dados de FMEA. Elas oferecem funcionalidades que automatizam cálculos e geram relatórios detalhados, tornando o processo mais eficiente e menos propenso a erros manuais.
Adotar essas práticas potencializa o impacto do FMEA, permitindo que as empresas não apenas previnam falhas, mas também melhorem continuamente a qualidade de seus processos industriais.
Desafios na Aplicação do FMEA
A implementação do FMEA em processos industriais enfrenta diversos desafios que podem dificultar sua eficácia.
Um dos principais obstáculos é a resistência à mudança organizacional. Equipes acostumadas a métodos tradicionais podem hesitar em adotar novas abordagens. Para mitigar essa resistência, é vital promover treinamentos e workshops que demonstrem os benefícios do FMEA, assegurando que todos compreendam o valor agregado ao processo.
Outra barreira significativa são as limitações de recursos. A aplicação do FMEA requer tempo e dedicação de profissionais qualificados. Em organizações com restrições orçamentárias, priorizar a alocação de recursos é fundamental. Uma solução prática é integrar a análise FMEA em etapas existentes de revisão de processos, otimizando tempo e esforço.
Por último, a complexidade do processo pode desencorajar a aplicação do FMEA. A análise detalhada dos modos de falha exige uma abordagem sistemática e meticulosa. Para enfrentar esse desafio, o uso de softwares especializados pode simplificar o processo, fornecendo ferramentas que automatizam cálculos e geram relatórios precisos.
Superar esses desafios é essencial para maximizar os benefícios do FMEA na prevenção de falhas e na melhoria contínua dos processos industriais.
Futuro do FMEA
O FMEA continua a evoluir com tendências emergentes que prometem transformá-lo significativamente. A integração de metodologias ágeis no FMEA está ganhando espaço, permitindo análises mais dinâmicas e adaptáveis às mudanças rápidas do mercado.
O impacto das novas tecnologias é notável. Tecnologias como inteligência artificial e machine learning estão sendo incorporadas para automatizar a identificação de modos de falha, tornando o processo mais eficiente e preciso. Isso não apenas acelera as análises, mas também melhora a qualidade dos resultados.
A continuidade do FMEA como ferramenta essencial depende da inovação contínua. As indústrias devem buscar constantemente novas maneiras de integrar o FMEA com outras práticas de gestão de qualidade. A adoção de software especializado é um passo crucial para garantir que o FMEA permaneça relevante e eficaz em um cenário industrial em constante transformação.
Conclusão
Ao longo deste artigo, discutimos a relevância do FMEA na identificação e mitigação de falhas em processos industriais. A análise dos modos de falha e seus efeitos é crucial para reduzir riscos, melhorar a qualidade dos produtos e aumentar a satisfação do cliente.
A contínua importância do FMEA se reflete na sua capacidade de se adaptar às novas tecnologias e tendências emergentes. Isso reforça o seu papel indispensável em um ambiente industrial em constante evolução.
Convidamos as organizações a implementarem o FMEA como parte de sua estratégia de qualidade. Ao adotar essa prática, as empresas estarão mais bem equipadas para enfrentar desafios futuros e garantir operações mais seguras e eficientes.
Créditos das fotos: https://depositphotos.com/br/
0 comments
Write a comment