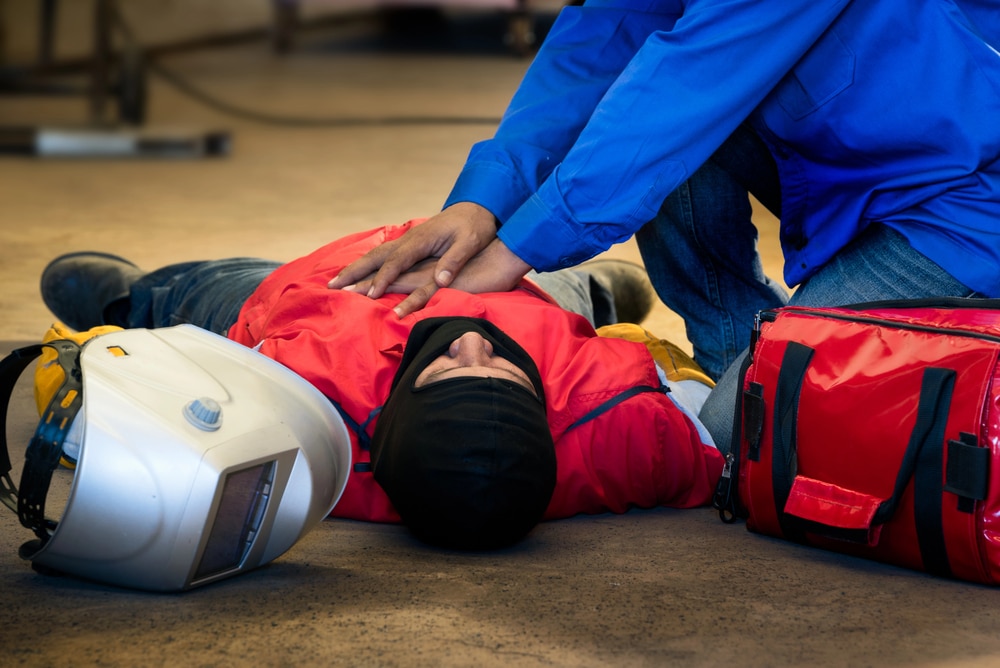
10 Causas Comuns De Acidentes Industriais E Como Evitá-los
Acidentes industriais são eventos não planejados que ocorrem em ambientes de trabalho, resultando em lesões, doenças ou danos materiais. Esses incidentes frequentemente derivam de erros humanos, falhas de equipamentos ou condições de trabalho inseguras. Estatísticas indicam que milhares de acidentes ocorrem anualmente, impactando negativamente trabalhadores e empresas.
Introdução aos Acidentes Industriais
Para os trabalhadores, as consequências podem ser severas, incluindo lesões e incapacidades. Para as empresas, os acidentes podem resultar em atrasos na produção e penalidades legais. Desta forma, a prevenção é essencial para proteger vidas e assegurar a continuidade dos negócios.
Fatores Humanos em Acidentes
Falta de Treinamento Adequado
Um dos principais fatores que contribuem para acidentes industriais é a falta de treinamento adequado. Trabalhadores que não recebem instruções claras sobre como operar máquinas ou executar tarefas com segurança estão mais propensos a cometer erros. Por exemplo, um funcionário sem treinamento apropriado pode não saber como reagir em situações de emergência, aumentando o risco de lesões.
Efeitos da Fadiga e Estresse
A fadiga e o estresse são inimigos silenciosos em ambientes industriais. Trabalhadores que enfrentam longas jornadas ou condições de trabalho estressantes podem ter sua concentração comprometida. Isso leva a lapsos de atenção e aumenta a probabilidade de acidentes. Um operador de máquina exausto, por exemplo, pode facilmente cometer um erro crítico durante a operação.
Não Cumprimento dos Procedimentos de Segurança
O não cumprimento dos procedimentos de segurança é outra causa comum de acidentes. Muitas vezes, por pressa ou desconhecimento, trabalhadores ignoram normas essenciais, como o uso de equipamentos de proteção individual (EPIs). Um exemplo prático é um funcionário que, ao não usar luvas de proteção, se expõe a riscos desnecessários durante o manuseio de materiais perigosos.
Falhas Mecânicas e Técnicas
As falhas mecânicas e técnicas são causas frequentes de acidentes em ambientes industriais. Equipamentos mal conservados ou desatualizados podem falhar em momentos críticos, colocando em risco a segurança dos trabalhadores.
Problemas comuns com equipamentos incluem:
- Manutenção inadequada, que pode resultar em peças desgastadas ou sistemas mal calibrados.
- Máquinas defeituosas ou desatualizadas, que não apenas reduzem a eficiência, mas também aumentam o risco de falhas inesperadas.
- Falta de proteções em máquinas perigosas, o que expõe os operadores a riscos desnecessários de lesões.
Para minimizar esses riscos, é essencial implementar um programa de manutenção preventiva eficaz. Isso inclui inspeções regulares, substituição de peças desgastadas e atualizações tecnológicas nos equipamentos. Além disso, é importante garantir que todas as máquinas estejam equipadas com proteções adequadas, como barreiras de segurança e dispositivos de desligamento automático.
Adotar essas práticas pode não apenas reduzir a incidência de acidentes, mas também prolongar a vida útil dos equipamentos e aumentar a produtividade geral da empresa.
Questões Ambientais e Organizacionais
O ambiente físico desempenha um papel crucial na segurança no trabalho. Iluminação e ventilação inadequadas podem comprometer a visibilidade e a qualidade do ar, aumentando o risco de acidentes. Ambientes mal iluminados dificultam a identificação de perigos, enquanto a falta de ventilação pode levar ao acúmulo de vapores tóxicos.
Níveis de ruído elevados são outra preocupação comum em ambientes industriais. Ruídos excessivos podem afetar a concentração dos trabalhadores, além de causar danos auditivos a longo prazo. A implementação de barreiras acústicas e o uso de protetores auriculares ajudam a mitigar esse problema.
O layout do ambiente de trabalho também é fundamental para a segurança. Um layout inseguro, com corredores estreitos ou obstruídos, pode resultar em quedas ou colisões. Para promover a segurança, é importante garantir que caminhos de circulação estejam sempre livres e bem sinalizados. Áreas de risco devem ser claramente delimitadas, e o armazenamento de materiais deve ser planejado para evitar quedas.
Adotar essas práticas contribui para um ambiente de trabalho mais seguro, reduzindo a probabilidade de acidentes e melhorando o bem-estar geral dos funcionários.
Escorregões, Tropeços e Quedas
Escorregões, tropeços e quedas são acidentes frequentes em ambientes industriais, frequentemente resultantes de pisos molhados e objetos fora do lugar. Em locais onde líquidos são manuseados, é comum ocorrer derramamentos que, se não limpos imediatamente, tornam o piso escorregadio, aumentando o risco de quedas.
Objetos deixados fora do lugar, como ferramentas ou materiais, também contribuem significativamente para tropeços. Esses acidentes não são apenas comuns, mas também perigosos, representando cerca de 15% das lesões em ambientes de trabalho, segundo dados de segurança ocupacional.
Para prevenir esses incidentes, é essencial adotar práticas como limpeza imediata de derramamentos e organização rigorosa das áreas de trabalho. Sinalizar pisos molhados e garantir que corredores estejam desobstruídos são medidas simples, mas eficazes para minimizar riscos.
Queimaduras e Exposição a Produtos Químicos
Queimaduras em ambientes industriais frequentemente ocorrem devido ao manuseio inadequado de substâncias perigosas, como ácidos e solventes. Os trabalhadores podem sofrer queimaduras químicas ao entrar em contato direto com esses materiais ou inalar vapores tóxicos. Tais acidentes não apenas causam lesões na pele, mas também podem afetar gravemente a saúde respiratória.
Para evitar esses riscos, é crucial implementar medidas de proteção eficazes. O uso de Equipamentos de Proteção Individual (EPIs) é fundamental. Entre os EPIs recomendados estão:
- Luvas resistentes a produtos químicos
- Aventais ou uniformes de proteção
- Máscaras faciais e protetores oculares
Além disso, treinamentos regulares em segurança química e o conhecimento das fichas de dados de segurança são essenciais para garantir a proteção dos trabalhadores e a redução de acidentes.
Eletrocussão e Segurança Elétrica
A fiação defeituosa é uma das principais causas de eletrocussão em ambientes industriais. Cabos desgastados ou mal isolados podem resultar em choques elétricos graves. Além disso, o uso inadequado de ferramentas elétricas aumenta o risco de acidentes, especialmente quando os equipamentos são operados sem a devida inspeção ou manutenção.
Para minimizar esses riscos, é essencial adotar práticas seguras de manuseio elétrico. Certifique-se de:
- Inspecionar regularmente a fiação e substituí-la se necessário.
- Usar ferramentas elétricas de acordo com as instruções do fabricante.
- Garantir que todos os trabalhadores tenham treinamento adequado em segurança elétrica.
Fique atento aos sinais de alerta, como faíscas, choques leves ou cheiro de queimado, que indicam problemas elétricos. A resposta rápida a esses sinais pode prevenir acidentes mais graves.
Ferimentos por Máquinas
Os ferimentos por máquinas são uma preocupação constante em ambientes industriais, especialmente durante a operação de equipamentos pesados. Máquinas como prensas, guindastes e empilhadeiras, quando mal operadas, podem causar lesões graves aos trabalhadores. A falta de atenção ou um momento de distração pode resultar em acidentes sérios.
Além disso, o uso de equipamentos inseguros agrava ainda mais esses riscos. Máquinas sem manutenção adequada ou com dispositivos de segurança ausentes podem falhar inesperadamente, colocando em perigo todos ao redor.
Para evitar tais incidentes, é crucial seguir diretrizes de operação segura. Isso inclui a inspeção regular das máquinas, garantindo que todos os componentes de segurança estejam funcionais. Treinamento adequado para os operadores também é essencial, assegurando que eles compreendam os riscos e saibam como evitá-los durante a operação diária.
Queda de Objetos
A queda de objetos é uma causa frequente de acidentes industriais, representando riscos significativos para a segurança dos trabalhadores. Ferramentas mal fixadas em áreas de trabalho e materiais armazenados em altura podem cair acidentalmente, resultando em ferimentos graves ou até fatais.
Para mitigar esses riscos, é essencial implementar medidas preventivas eficazes. Certifique-se de que todas as ferramentas estejam adequadamente fixadas e verificadas regularmente. Além disso, ao armazenar materiais em altura, utilize suportes e prateleiras que possam suportar o peso e a quantidade dos objetos armazenados.
Instruções claras e treinamento adequado para os trabalhadores sobre as práticas seguras de armazenamento e manuseio de ferramentas são igualmente importantes. Ao adotar essas ações, é possível reduzir significativamente a ocorrência de acidentes relacionados à queda de objetos no ambiente industrial.
Consequências para Trabalhadores
Os acidentes industriais podem ter consequências sérias para os trabalhadores, incluindo lesões e incapacidades. Segundo dados do Ministério da Saúde, cerca de 700 mil acidentes de trabalho são registrados anualmente no Brasil, muitos resultando em lesões permanentes. Isso pode levar à perda de capacidade funcional, afetando a qualidade de vida e a capacidade de sustento do trabalhador.
Além das consequências físicas, o impacto psicológico de um acidente não deve ser subestimado. Os trabalhadores podem enfrentar estresse pós-traumático, ansiedade e depressão após um incidente. A experiência de um acidente pode gerar medo de retornar ao trabalho ou insegurança em suas funções habituais. Esses efeitos emocionais, se não tratados, podem prejudicar tanto a saúde mental quanto o desempenho profissional do trabalhador.
Consequências para Empresas
Os acidentes industriais podem causar atrasos na produção, afetando diretamente a capacidade de uma empresa de cumprir prazos e atender demandas de clientes. Por exemplo, uma indústria automobilística pode enfrentar interrupções significativas se um acidente paralisar uma linha de montagem.
Ainda, as penalidades legais são uma preocupação constante. Empresas que não cumprem as normas de segurança podem ser multadas ou enfrentar processos judiciais. Um exemplo notório é o da Samarco, que após o desastre em Mariana, enfrentou pesadas penalidades financeiras.
Além disso, os danos à reputação são uma consequência grave e duradoura. A confiança dos clientes e parceiros pode ser abalada, impactando negativamente as vendas e contratos futuros. Empresas como a BP, após o vazamento de petróleo no Golfo do México, sofreram intensas críticas e viram sua imagem desgastada globalmente.
Impacto na Sociedade
Os acidentes industriais têm um impacto econômico significativo na sociedade, principalmente devido aos custos com saúde. Estima-se que, anualmente, bilhões de reais são gastos no tratamento de feridos em ambientes industriais. Esses custos incluem despesas hospitalares, reabilitação e medicamentos, pressionando o sistema de saúde pública.
Adicionalmente, o impacto na previdência social é notável. Acidentes podem resultar em afastamentos prolongados do trabalho, aumentando o número de benefícios pagos, como auxílio-doença e aposentadorias por invalidez. Segundo dados do INSS, cerca de 10% dos benefícios concedidos estão relacionados a acidentes de trabalho.
Esses fatores não apenas oneram os cofres públicos, mas também afetam a economia, reduzindo a produtividade e causando perdas financeiras significativas para a sociedade como um todo.
Importância do Treinamento e Conscientização
A capacitação contínua dos trabalhadores é crucial para a prevenção de acidentes industriais, garantindo que todos estejam atualizados sobre as melhores práticas de segurança. Programas de treinamento eficazes incluem instruções detalhadas sobre o uso correto de equipamentos e a importância de seguir protocolos de segurança.
Além disso, as simulações de emergência são essenciais para preparar os funcionários para situações inesperadas. Essas simulações ajudam a identificar possíveis falhas nos procedimentos e melhoram a resposta rápida em caso de acidentes reais. Um exemplo de programa eficaz é a realização de exercícios de evacuação, que treinam os trabalhadores a saírem do local de forma segura e organizada.
Essas práticas não só reforçam a segurança no ambiente de trabalho, mas também promovem uma cultura de conscientização, onde todos se sentem responsáveis pela própria segurança e pela segurança dos colegas.
Uso de Equipamentos de Proteção
O uso de Equipamentos de Proteção Individual (EPIs) é fundamental para minimizar os riscos de acidentes no ambiente industrial. Esses equipamentos são obrigatórios e devem ser utilizados sempre que necessário para garantir a segurança dos trabalhadores.
Entre os EPIs essenciais, destacam-se:
- Capacetes de segurança: Protegem contra impactos e quedas de objetos.
- Luvas de proteção: Evitam cortes, queimaduras e contato com produtos químicos.
- Óculos de segurança: Protegem os olhos de partículas e substâncias nocivas.
- Protetores auriculares: Reduzem danos auditivos em ambientes com alto nível de ruído.
É crucial que os trabalhadores sejam instruídos sobre as diretrizes de uso adequadas, garantindo que os EPIs estejam sempre em perfeito estado e ajustados corretamente. A conscientização sobre a importância dos EPIs deve ser constante, reforçando a responsabilidade individual e coletiva na prevenção de acidentes.
Políticas de Segurança no Trabalho
Estabelecer políticas de segurança no trabalho é essencial para prevenir acidentes industriais. Essas políticas devem ser claras, abrangentes e adaptadas às condições específicas de cada ambiente. A criação dessas diretrizes envolve a análise dos riscos potenciais e a implementação de protocolos de segurança que orientem as ações dos trabalhadores.
Exemplos de políticas eficazes incluem a obrigatoriedade do uso de Equipamentos de Proteção Individual (EPIs), a definição de zonas seguras e a padronização dos procedimentos de emergência. Além disso, é crucial realizar monitoramento e auditoria regulares para garantir que as políticas sejam seguidas corretamente e para identificar áreas de melhoria.
Incentivar a participação dos trabalhadores no desenvolvimento e revisão dessas políticas pode aumentar a eficácia das medidas de segurança, promovendo um ambiente de trabalho mais seguro e colaborativo.
Conclusão e Reflexão Final
Prevenir acidentes industriais é essencial para proteger trabalhadores e garantir a continuidade operacional das empresas. Identificamos causas comuns, como falhas humanas e técnicas, e propusemos medidas de prevenção. A implementação de práticas seguras, como o uso de EPIs e treinamentos contínuos, é crucial.
É fundamental fomentar uma cultura de segurança, onde cada colaborador se sinta responsável pela sua segurança e pela dos colegas. Investir nessas práticas não apenas reduz riscos, mas também fortalece a reputação e a sustentabilidade das organizações.
Créditos das fotos: https://depositphotos.com/br/
0 comments
Write a comment