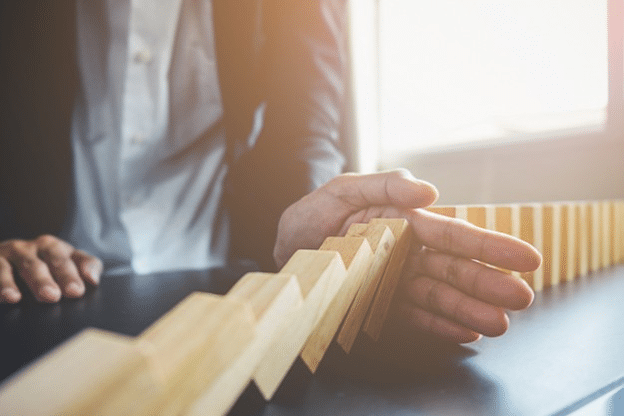
FMEA: o que é e como fazer para reduzir falhas na sua companhia
Você aplica o processo FMEA no controle de qualidade da sua empresa? Ainda não? Pois saiba que a análise dos modos de falha e seus efeitos é uma das ferramentas mais eficientes para ajudar a reduzir os erros e melhorar a qualidade de seus produtos.
Portanto, se você deseja garantir a satisfação e confiança do cliente, precisa entender como esse método funciona e adotá-lo em sua estratégia de gestão.
Por falhas entendemos qualquer erro ou defeito, real ou potencial, que um processo pode apresentar e que pode, eventualmente, chegar ao consumidor final. Exatamente o que precisamos evitar para garantir a qualidade do produto ou serviço prestado, independentemente de qual ele for.
Diante desse cenário competitivo que vivemos, ferramentas de controle da qualidade vêm sendo cada vez mais utilizadas de forma estratégica pelas empresas, transpondo o limite de garantia de pós-venda.
Por isso, confira o conteúdo e descubra os dois tipos de FMEA, quais são as suas vantagens e um passo a passo para aplicá-lo na qualidade. Boa leitura!
FMEA: o que é e onde aplicar
O FMEA (Failure Mode and Effect Analysis ou análise dos modos de falha e seus efeitos) é um método usado para identificar todas as falhas possíveis no processo de produção de um produto, bem como as suas principais causas e consequências.
Desse modo, ele permite identificar os possíveis problemas e seus impactos em toda a entrega, desde os primeiros passos do projeto e permanecendo durante toda a vida útil do produto ou serviço.
O objetivo do método FMEA é priorizar os problemas conforme a gravidade das consequências, a frequência da ocorrência e a facilidade de detecção.
Por fim, estabelecer ações para eliminar ou reduzir a sua ocorrência, aumentando a produtividade e a qualidade do produto final.
Portanto, ajuda na prevenção de falhas e na análise dos riscos de um processo, através da definição de causas e efeitos para elaboração de estratégias que deverão ser realizadas para inibir as falhas.
O método pode ser utilizado:
- Durante a projeção ou remodelagem de um processo, produto ou serviço;
- Antes do desenvolvimento de planos de um processo novo ou modificado;
- Para analisar falhas de um processo, produto ou serviço existente.
Tipos de FMEA
Apesar de o objetivo principal ser sempre o mesmo, identificar falhas, existem vários tipos de FMEAS, que se diferenciam pela especificidade de atuação, forma de classificar os riscos e nomes dados aos elementos.
Os tipos mais comuns são:
- FMEA de Produto (ou de projeto): analisa as falhas que podem ocorrer nas especificações do produto focando em componentes;
- FMEA de Processos: identifica falhas no planejamento e execução do processo;
- FMEA de Sistema: foca nas funções globais de sistemas;
- FMEA de Serviço: mira nos em processos de manufatura e montagem;
- FMEA de Software: é direcionado para funções de software;
- FMEA de Design: explora falhas de mau funcionamento do produto, que podem reduzir a vida útil, bem como preocupações regulatórias e de segurança;
- FMEA de processos administrativos: considera todas as etapas de um processo sob a ótica administrativa.
Vantagens do FMEA
O FMEA atua, muitas vezes, como medida preventiva. Dessa forma, a principal vantagem do método é a redução da frequência de falhas, ou até mesmo, a eliminação das mesmas. Além disso, ele proporciona:
- Aumento da confiabilidade de produtos ou processos em operação;
- Economia de custos e materiais;
- Menos riscos de erros e mais qualidade em procedimentos administrativos;
- Mais assertividade e qualidade de produtos e processos;
- Maior satisfação dos clientes.
Passo a passo para aplicar na Gestão de Qualidade
Tão importante quanto saber teoricamente o que é FMEA, é aprender na prática como aplicá-lo na qualidade.
A seguir montamos um passo a passo fácil para uma aplicação básica do FMEA. Use esse material como guia e faça as adaptações necessárias à realidade da sua empresa, a fim de otimizar resultados. Confira!
1. Monte um time diversificado
Selecione profissionais com conhecimento sobre o processo e as necessidades do cliente para compor a equipe de análise. Prefira escolher pessoas de diferentes áreas como, por exemplo, marketing, vendas, design, produção, qualidade, entre outras.
2. Identifique as falhas possíveis
Defina quais são as falhas mais prováveis de ocorrer e quais já estão acontecendo dentro de um sistema. Utilize fluxogramas para identificar o fluxo de trabalho e fazer a análise de cada etapa do processo e da produção.
Pode ser interessante dividir esse passo em partes menores para compreender melhor os processos de cada setor, como, por exemplo: fábrica, estoque, design, produção, gestão, transporte.
3. Entenda como as falhas ocorrem
Para cada função e em cada fase, descreva a forma como a falha pode acontecer. Se for preciso, retorne aos passos anteriores para reescrever o processo mais detalhadamente para garantir a compreensão dos modos de falha e assim evitá-las.
4. Defina consequências
Todas as falhas identificadas implicam em consequências internas que afetam o processo, o sistema, os produtos e os serviços.
Os efeitos da falha podem também atingir o cliente. Nesse caso, é importante identificar o tipo de experiência que o cliente tem ou pode ter devido a falha e o que acontece quando esta falha ocorre.
5. Faça uma análise da gravidade das consequências
A gravidade de uma falha (S), assim como as chances de ocorrência, devem ser medidos em uma escala de 1 a 10, considerando 1 como gravidade insignificante e 10 uma consequência catastrófica.
6. Identifique as causas desses problemas
Determinar a razão para uma falha ter ocorrido é tão vital quanto avaliar as suas consequências. Para cada falha existe uma causa e identificar a origem do problema é parte fundamental do processo de tentar evitar que ela ocorra novamente.
7. Meça o potencial de ocorrência
Assim como ocorre com a gravidade da consequência de uma falha, o potencial de ocorrência (O) também deve ser medido considerando uma escala de 1 a 10, sendo 1 extremamente improvável e 10 inevitável.
8. Realize uma classificação de detecção
A classificação de detecção (D) estima a probabilidade de detectar a causa ou seu modo de falha depois que ela já ocorreu, porém antes de chegar a afetar o cliente final.
A detecção leva em consideração a escala de 1 a 10, sendo 1 certeza absoluta do problema ser detectado antes de atingir o cliente e 10 que o controle de qualidade não detecta o problema.
9. Calcule a prioridade de risco
Esse cálculo é feito pela fórmula: S × O × D (passos 5, 7 e 8). O valor auxilia a classificação das falhas na ordem em que devemos priorizar a resolução.
10. Defina as resoluções e ações recomendadas
Com os dados analíticos em mãos, a equipe precisa agir para criar estratégias que otimizem os processos com foco em diminuir a gravidade das consequências e o potencial de ocorrência.
É interessante definir os responsáveis por cada ação e estabelecer datas de implementação de cada melhoria.
11. Mantenha um monitoramento
Conforme as estratégias são desenvolvidas, é necessário fazer o acompanhamento dos resultados, incluindo a data no formulário de FMEA.
Pronto para aplicar o que é FMEA na qualidade? O método é uma valiosa ferramenta valiosa para otimizar o processo de produção, atrair maior confiabilidade ao produto e serviço e aumentar a satisfação do cliente.
Comece agora mesmo e deixe nos comentários os resultados dessa experiência.
0 comments
Write a comment